Permeable Pavers and Pavements
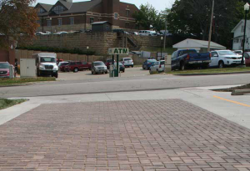

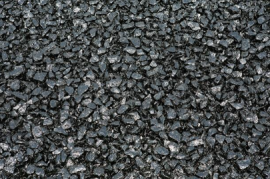
Brief Description
Permeable pavements allow stormwater runoff to filter through surface voids into an underlying stone reservoir for temporary storage and/or infiltration. The most commonly used permeable pavement surfaces are pervious concrete, porous asphalt, and permeable interlocking concrete pavers (PICP). Permeable pavements have been used for areas with light traffic at commercial and residential sites to replace traditional impervious surfaces in low-speed roads, alleys, parking lots, driveways, sidewalks, plazas, and patios. While design details vary, all permeable pavements have a similar structure, consisting of a surface pavement layer, an underlying stone aggregate reservoir layer, optional underdrains and geotextile over uncompacted soil subgrade.
Cost Range
Construction: $$-$$$
O&M: $$
Ideal Conditions for Installation
Precipitation: Suitable for most storm events
Soils: Works well in A & B soils with no underdrain; can work in C & D soils with an underdrain system
Groundwater: 3 foot separation from bottom of permeable pavement reservoir to season high water table.
Where/Applicability
Residential: Yes
Commercial: Yes
Ultra Urban: Yes
Industrial: Limited to areas with low to moderate pollutant loading potential
Highway/Road: Yes, in non-travel lane areas
Retrofit: Yes, but typically requires total replacement of surface improvements when used
Feasible: Do not use when water table is less than 4 feet deep, do not use over impervious soil
Maintenance
Frequency: Quarterly at first, adjust as needed
Type: Vacuuming
Monitoring: Visual observation, time to drain surface
Permit Renewal: No permit needed
Performance
Total Suspended Solids (TSS): High
Chloride: Medium
Total Nitrogen: High in solid form, Medium in dissolved
Metals: High
Oils and Grease: High
Pathogens: Medium
Phosphorus: High
Specifications
Pretreatment is recommended to remove sediments and floatables.
Follow manufacturer recommendations for any specific or proprietary products.
1. Excavate carefully to avoid subgrade compaction
2. Excavate as flat as possible
3. Excavation should work from the sides, outside the footprint of the infiltration area
4. Keep bottom of excavation at least 3 feet above seasonal water table
5. Keep at least a 10 foot setback from all structure foundations
6. Maintain appropriate setbacks from well heads (100 foot minimum for culinary wells, 50 foot from other wells)
7. Typically use geotextile between native soils and stone subbase
8. Compact stone subbase (typically No. 57 sized aggregate) with roller until there is no visible movement of the aggregate
9. May require graded material between pavement and stone subbase
10. Install pervious concrete or pervious asphalt according to manufacturer’s recommendations
Design Notes:
1. Soils - soil conditions and infiltration rates determine the use of an underdrain. (Nrcs hydrologic soils , group (HSG) C or D usually require an underdrain whereas HSG A and B soils do not.) Designers should evaluate existing soil properties during initial site layout with the goal of configuring permeable pavement that conserves and protects soils with the highest infiltration rates. In particular, areas of HSG A or B soils should be considered as primary locations for all types of infiltration practices.
2. In most cases, permeable pavement should not be situated above fill soils. Designs in compacted fill soils may require an impermeable liner and an underdrain. Permeable pavements should only be placed on fill.
3. Contributing drainage area - permeable pavements sometimes capture runoff from adjacent areas, pavements, and roofs, runoff from permeable areas is not recommended due to potential clogging of the permeable pavement. The at-grade contributing drainage area into permeable pavement should generally not exceed twice the surface area of the permeable pavement. This guideline helps reduce the rate of surface sedimentation. The 2:1 ratio can be increased to no greater than 5:1 if at least one of these conditions exist.
a. Permeable pavement is receiving runoff from roofs as it tends to be very low in sediment; or
b. Runoff from adjacent impervious surfaces remains unburdened with sediment due to effective pretreatment prior to entering the permeable pavement.
4. Permeable pavement and contributing impervious pavements are assumed to receive regular vacuuming to reduce and control sediment loads and surface clogging potential.
5. Soil subgrade slope - the slope of the soil subgrade should be as flat as possible (i.e. Less than 1 percent longitudinal slope) to enable even distribution of stormwater. Lateral slopes should be less than percent.
6. Soil subgrade compaction - this should be avoided wherever possible to maximize infiltration. In some situations, compaction may be needed for supporting vehicular loads. In such cases compaction density and subsequent soil infiltration should be assessed in a test pit(s) on the site to determine an acceptable soil density and its contribution to soil strength and infiltration.
7. Excavation methods - excavation should be conducted in a manner that minimizes soil subgrade compaction. Tracked rather than wheeled equipment is recommended working from the sides of the excavation.
8. Surface slopes - surface slopes for all permeable pavement types should be at least 1percent to provide an alternative means for drainage should the surface become completely clogged due to lack of maintenance. Designs should provide an alternative means for stormwater to enter the aggregate reservoir if the pavement surface should ever become clogged, for extreme storm events.
9. Overflow structures - permeable pavements are not designed to store and infiltrate all stormwater from all storms. Therefore, an outlet or outlets are required to prevent water from rising into and over the surface.
10. Minimum depth to seasonal high water table - a high groundwater table may cause seepage into the bottom of permeable pavement and prevent complete drainage. Also, soil acts as a filter for pollutants between the bottom of the pavement base and the water table. Therefore a minimum vertical separation of 3 feet is required between the bottom of the permeable pavement reservoir layer and the seasonal high groundwater table.
11. Setbacks - to avoid harmful seepage. Permeable pavement should not be hydraulically connected to building foundation unless an impermeable liner is placed against the foundation or basement wall. Even under these circumstances, great care should be taken to avoid creating a wet basement problem. If there is no liner, the permeable pavement base should be 10 feet or greater from structures (epa recommends a minimum setback from building foundations of 10 down-gradient and 100 feet up-gradient. See EPA factsheet "storm water technology fact sheet: porous pavement," EPA 832-f-99-023). Again, it is the designer's responsibility to avoid creating a wet basement problem. Likewise, permeable pavement bases should be hydraulically separated from adjacent road bases.
12. Permeable pavements without underdrains infiltrate stormwater and should follow requirements for wellhead protection (EPA recommends a minimum setback of 100 feet from water supply wells). Underground utility lines are best located away from permeable pavement bases. However, if they need to penetrate the base, consideration should be given to waterproofing (depending on utility) or possible encasement using low-strength flowable concrete fill. Setbacks can be reduced at the discretion of the local authority for designs that use underdrains and/or liners.
13. Informed owner - the property owner should clearly understand the unique maintenance responsibilities inherent with permeable pavement, particularly for parking lot applications. The owner should be capable of performing routine and long-term actions (e.g. Vacuuming) to maintain the pavement's hydrologic functions, and avoid future practices (e.g., Winter sanding, seal coating or repaving) that diminish or eliminate them. For porous asphalt a diluted emulsion fog can be used as needed. Maintenance agreements, covenants, maintenance easements for performance bonds are encouraged between the local authority and the property owner.
14. Permeable pavements should not be used in high pollutant loading sites. High pollutant loading sites are those that receive constant sediment or trash and/or debris. Places where fuels and chemicals are stored or handled can be potential stormwater hotspots and permeable pavement should not be constructed in these places, likewise, areas subject to wind borne dust and sediment should not use permeable pavement unless the pavement can be vacuumed regularly. The following limitations should be considered before utilizing permeable pavements in any design.
15. Permeable pavement is suitable for pedestrian-only areas, low-volume roads, low speed areas, overflow parking areas, residential driveways, alleys, and parking stalls. These can be residential collector roads or other applications with similar traffic loads.
16. Permeable pavement can be prone to clogging from sand and fine sediments that fill void spaces and the joints between pavers. As a result, it should be used carefully where frequent winter sanding is necessary because the sand may clog the surface of the material. Periodic maintenance is critical, and surfaces should be cleaned with a vacuum sweeper at least two times a year.
17. Fuel may leak from vehicles and toxic chemicals may leach from asphalt and/or binder surface. Porous pavement systems are not designed to treat these pollutants.
Structural Design:
1. Permeable interlocking pavements (smith 2011) use flexible pavement design methods adapted from the 1993 AASHTO guide for design of pavement structures (AASHTO 1993) there has been limited research on full-scale testing of the structural behavior of open-graded bases used under permeable pavements to better characterizing relationships between loads and deformation. Therefore conservative values (i.e. AASHTO layer coefficients) should be assumed for open-graded base and subbase aggregates in permeable pavement design.
2. Structural design methods consider the following in determining surface and base thickness to support vehicular traffic:
a. Pavement life and total anticipated traffic loads expressed as 18,000 pounds equivalent singe axle loads or ESALs (this method as assessing loads account for the additional pavement wear caused by trucks)
b. Soil strength expressed as the soaked california bearing ratio (CBR), R-value or resilient modulus(MR)
3. Strength of the surfacing, base and subbase materials
4. Environmental factors including freezing climates and extended saturation of the soil subgrade.
3. Structural design for vehicular applications should generally be on soil subgrades with a cbr (96-hour soaked per ASTM d1883 or AASHTO t 193) of 4 percent, or a minimum r-value = 9 per ASTM d 2488 or AASHTO t-190, or a minimum mr of 6,500 pounds per square inch (45 mega pascals) per AASHTO t-307. Soils with lower strengths typically require thickened permeable bases or those using cement or asphalt stabilized open-graded aggregates.
4. Soil compaction required to achieve these soil strengths will reduce the infiltration rate of the soil. Therefore, the permeability or infiltration rate of soil should be assessed at the density required to achieve one of these values. If soils under vehicular traffic have lower strengths than those noted above, or are expansive when wet, there are several options including:
a. Underdrains
b. Thickened base/subbase layer(s)
c. Cement or asphalt stabilized base layer
d. Lime or cement stabilized (with design consideration given to practically no infiltration in such cases).
These options are typically used in combination. Pedestrian applications can be placed on lower strength soils than those noted.
Design for nutrient and TSS reductions:
Permeable pavements can be designed to reduce nutrient loadings to the ground of surface waters. The design needs to be specifically designed to capture phosphorus. The permeable pavement system can also be designed to capture nitrogen, although it is important to note that nitrogen and phosphorus each require specific designs to facilitate their removal from stormwater. The following paragraphs describe the design characteristics necessary for the removal of phosphorus and nitrogen.
A study by (bean2007a) showed higher nitrate concentrations in the exfiltrate compared to the infiltrate. Nitrogen reduction capabilities of permeable pavement can be enhanced in partial infiltration designs to detain water in the base/subbase for over 24 hours. This time is required to ensure complete de-nitrification occurs.
Permeable pavers can use specially coated aggregates in the joints and bedding and all systems can use them in the base to reduce phosphorus. Coated aggregates (sometimes called "engineered aggregates") have an effective life of seven to ten years and target the removal of dissolved phosphorous, according to manufacturers literature.
A filter layer made of sand or fine aggregate placed under or sandwiched within permeable pavement bases are occasionally used as a means to reduce nutrients. This layer can be enhanced with iron filing for phosphorous reduction (erickson 2010). Their effectiveness, initial cost, reduction in flow rates, and maintenance cost should be weighed against other design options for nutrient reductions. Sand filters will incur additional construction expense and this can be reduced by placing sand filters under the subbase at the down slope end of a permeable pavement. The disadvantage of sand filters is that they will eventually require removal and restoration if continued phosphorous reduction credit is desired. Concentrating their location in the down slope areas of the site can help reduce future maintenance costs and site disruptions. A second approach useful for nutrient and TSS reduction can occur on sloping sites by creating intermittent berms in the soil subgrade. These enable settlement of suspended solids and encourage de-nitrification if appropriately designed. A third alternative is using a "treatment train" approach where a permeable pavement initially filters runoff and the remaining water outflows to bioswales or rain gardens adjacent to the pavement for additional processing and nutrient reduction. There may be BMPs used to remove nutrients as the water moves through the watershed.
Maintenance:
1. Observation well - typically this consists of well-anchored, six-inch diameter perforated PVC pipe that extends vertically to the bottom of the reservoir layer. This is installed at the down slope end of the permeable pavement. The observation well should be fitted with a lockable cap installed flush with ground surface (or under the pavers) to facilitate periodic inspection and maintenance. The observation well enables visual monitoring of drawdown within the reservoir layer after a storm.
2. Overhead landscaping - some communities require a certain percentage of parking lots to be landscaped. Large-scale permeable pavement should be carefully planned to integrate landscaping in a manner that maximizes runoff treatment and minimizes risk of sediment, mulch, grass clippings, crushed leaves, nuts, and fruits inadvertently clogging the surface. Prior to construction, owners should commit to a vacuuming plan that includes vacuuming frequency and equipment needs. The vacuuming frequency depends on the time of year. In the spring, tree buds and seeds necessitate frequent vacuuming. In the fall, tree leaves and acorns necessitate frequent vacuuming. In the summer, vacuuming frequency depends on permeable pavement exposure to organic material from trees and nearby vegetated areas. Vacuuming equipment and methods for sediment removal are provided in the section addressing operation and maintenance.
Winter considerations:
Plowed snow piles should be located in adjacent grassy areas so the sediments and pollutants in snowmelt are partially treated before they reach all permeable pavements. Sand and salt are not recommended for winter traction over permeable pavements. A significant winter advantage of permeable pavements is that they require less deicing materials than their impervious counterparts. Use of deicing material on permeable pavements is therefore not recommended.
Signage:
Permeable pavements can be used as opportunities for public education with signs explaining how they work. Infiltration demonstrations also help show how the pavements work. Signs provide a reminder to maintenance crews of their presence and list maintenance do's and don'ts specific to the permeable pavement type.
Construction Sequence
Follow manufacturer recommendations for any specific or proprietary products.
General Guidelines:
1. Install all erosion and sediment control measures required by the SWPPP 2. Rough grade site where permeable pavement is to be constructed 3. Excavate carefully to bottom of subbase. Bottom of excavation should be flat
4. Scarify native soils to 4” deep 5. Place geofabric between native soils and stone subbase
6. Place and compact stone subbase
7. Top subbase with bedding or choker base for finished pavement as needed
8. Install surface layer of pervious concrete or asphalt according to manufacturer’s recommendations
Construction Notes:
1. Construction of the permeable pavement begins after the entire contributing drainage area has been stabilized. The proposed site should be checked for existing utilities prior to any excavation.
2. Temporary erosion and sediment controls are needed during installation to divert stormwater away from the permeable pavement area until it is constructed and contributing drainage areas have been stabilized by a uniform perennial vegetative cover with a density of at least 70 percent over the entire pervious surface area, or other equivalent means. Special protection measures such as erosion control fabrics may be needed to protect vulnerable side slopes from erosion during and after the excavation process. The proposed permeable pavement area must be kept free from sediment during the entire construction process.
3. Where possible excavation should work from the sides and outside the footprint of the permeable pavement area (to avoid soil compression). Contractors can utilize a "cell" construction approach whereby the proposed permeable pavement area is divided into 500 to 1000 square feet temporary cells with 10 to 15 feet wide earthen bridges between them so that the cells can be excavated from the side. Then the earthen bridges are removed. Excavated material should be placed away from the open excavation to maintain stability of the side walls.
4. The native soils along the bottom of the permeable pavement system can be scarified or tilled to a depth of 3 to 4 inches and graded prior to the placement of the aggregate.
5. Geotextile shall be installed on the sides of the reservoir as detailed.
6. Do not install pervious concrete or porous asphalt in rain or snow, and do not install frozen aggregate materials under any of the surfaces.
7. Construction materials contaminated by sediments must be removed and replaced with clean materials.
8. Moisten, place and level the APWA no. 1 clean sewer rock (APWA 31 05 13) subbase and compact it in minimum 12 inch thick lifts with four passes of a steel drum static roller until there is no visible movement. The first two passes are in vibratory mode and the final two passes in static mode. The filter aggregate should be moist to facilitate movement into the reservoir course.
9. Place edge restraints before the base layer, bedding and pavers are installed. Permeable interlocking pavement systems require edge restraints to prevent vehicle tires from moving the pavers. Edge restraints may be standard concrete curbs or curb and gutters.
10. Moisten place and level the APWA no 4 clean fill sewer rock (APWA 31 05 13) in a single lift (4 inches thick). Compact it into the reservoir course beneath with at least four (4) passes of a steel drum static roller until there is no visible movement. The first two passes are in vibratory mode, with the final two passes in static mode.
11. Place and screed the bedding course material (APWA no. 8 clean pea gravel 31 05 13)
12. Pavers may be placed by hand or with mechanical installation equipment.
13. Fill gaps at the edge of the paved areas with cut pavers or edge units. When cut pavers are needed, cut the pavers with a paver splitter or masonry saw. Cut pavers no smaller than one-third (1/3) of the full unit size if subject to tires.
14. Fill the joints and openings with no. 8 pea gravel (apwa 31 05 13). Sweep and remove excess gravel from the paver surface.
15. Compact and seat the pavers into the bedding course with a minimum low-amplitude 5,000lbf, 75 to 95 hz plate compactor. Do not compact within 6 feet of the unrestrained edge of the pavers.
16. Thoroughly sweep the surface after construction to remove all excess aggregate.
17. Inspect the area for settlement. Any paving units that settle must be rest and inspected.
18. The contractor shall return to the site within 6 months, or after first winter, to top up the paver joints with stones.
Downloads
Structural Design Guidelines for Porous Asphalt Pavements
Permeable Pavers DWG
Links
Porous Asphalt Reference
Pervious Concrete Pavement Reference
Storm Water Management by Pervious Concrete Reference
Permeable Pavers